What is Final Product Assembly?
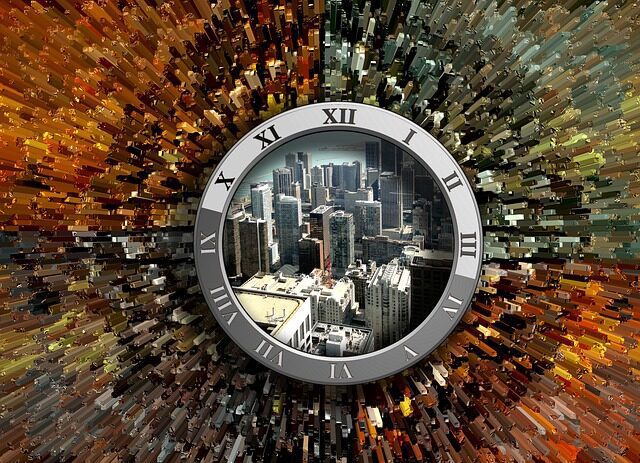
Final product assembly is the process of combining individual components and materials into a finished product during manufacturing. This crucial step in the manufacturing process involves various assembly methods or manufacturing processes, such as automated machinery, robotic assembly, and manual assembly. The goal is to streamline manufacturing processes and supply chain management to bring products to market faster by increasing efficiency and quality control. This process is essential for producing a quality product that meets customer expectations.
One important aspect of many industries in final product assembly is the bill of material (BOM), which is a multilevel BOM or a top-level bill of material that lists all the components required to assemble a product. These components can be mechanical, electrical, or software-based, and the BOM helps ensure that all necessary parts are available for the process. This system is crucial for maintaining the quality and efficiency of the assembly process. A mechanical assembly drawing may also be used to guide the mechanical assembly of components, ensuring the final product is produced correctly and meets the required quality standards.
The Different Types of Assembly Lines in Final Product Assembly
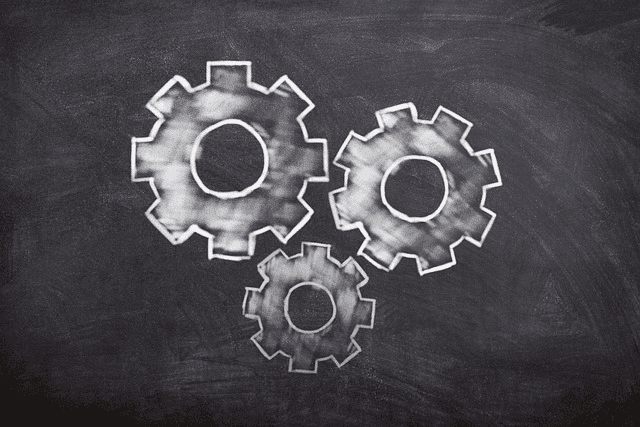
To optimize the process, manufacturers often employ assembly lines, which are designed to efficiently move components through the various stages of production. These assembly lines may be comprised of different types of equipment, such as machines, robots, and human workers, each performing a specific task in the process.
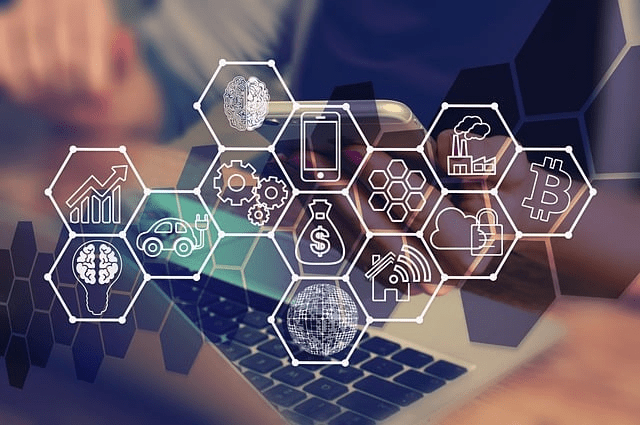
Effective supply chain management is also essential for successful final products assembly. This involves coordinating the procurement and delivery of materials and components from suppliers to ensure that they arrive at the right time and in the right quantities. By carefully managing the manufacturing supply chain, companies can reduce costs, minimize waste, and improve overall efficiency.
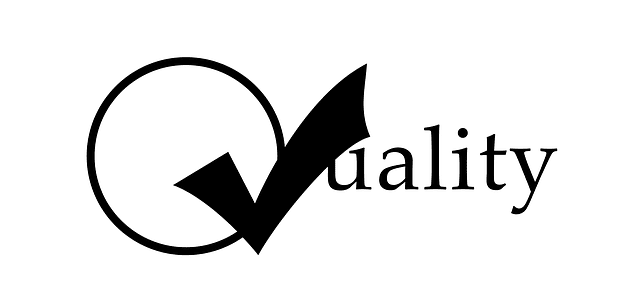
Quality control is another critical aspect of final products assembly. This involves implementing best practices for manufacturing, such as regular testing and inspection of components and finished product, to ensure that they meet the required quality standards. By catching defects early in the process, manufacturers can save time and money by avoiding costly rework or product recalls.
How to Choose the Right Final Product Assembly Process Company?
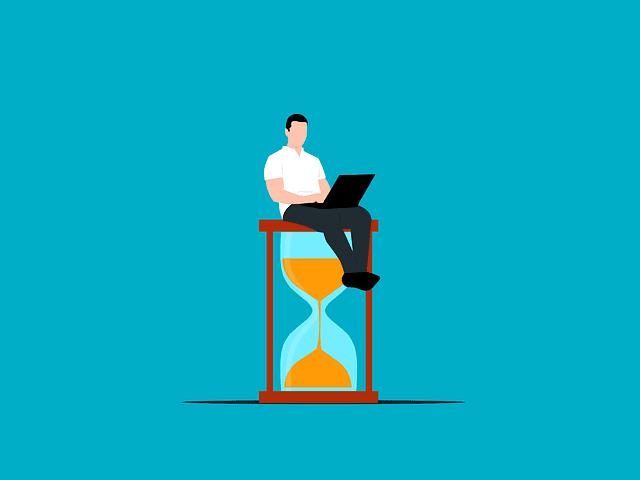
When selecting a final product assembly company, there are several factors to consider:
Experience and expertise: Look for a company with a proven track record of successfully assembling products similar to yours. They should have the necessary knowledge and skills to handle your specific assembly requirements, ensuring the final product meets customer expectations.
Quality control measures: Ensure that the company has a robust quality check system in place to guarantee the consistency and reliability of the finished product. This may include regular testing, inspection, and adherence to manufacturing industry standards, ensuring a quality product is produced.
Capacity and scalability: Choose a company that has the capacity to handle your current production needs and the ability to scale up as your business grows. They should have the necessary equipment, workforce, and infrastructure to accommodate your requirements, facilitating business growth and future planning.
Location and logistics: Consider the company’s location and its proximity to your target markets. This can impact shipping costs and lead times. Additionally, evaluate their logistics capabilities to ensure they can efficiently manage the transportation and delivery of your products, reflecting effective supply chain management.
Technology and innovation: Select a company that invests in the latest technology and continuously innovates its assembly processes. This can help streamline operations, reduce costs, and improve product quality, ensuring the end product meets industry standards and customer expectations.
Customer service and communication: Choose a company that values open communication and provides excellent customer service. This ensures that your needs and feedback are addressed promptly, fostering a positive relationship and ensuring the final product aligns with customer expectations.
Factors to Consider When Choosing a Final Assembly of Product
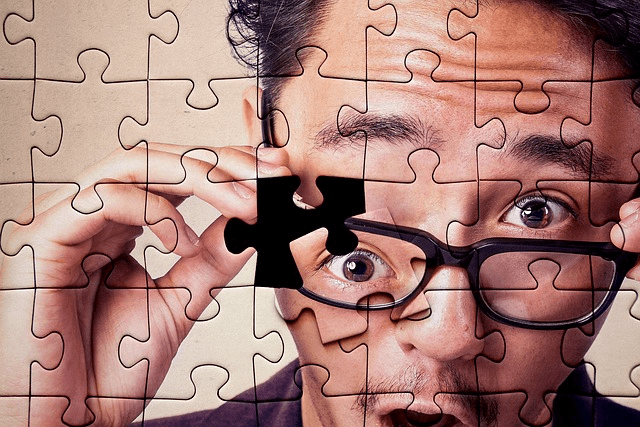
In addition to selecting the right assembly company, there are several factors to consider when planning your final product assembly process:
Assembly method: Determine the most suitable assembly method for your final product, whether it’s automated, manual, or a combination of both. Consider factors such as product complexity, volume, and cost when making this decision. This choice can significantly impact the overall efficiency and quality of the finished product.
Component sourcing: Identify reliable suppliers for your product assembly components and establish strong relationships with them. Ensure that they can consistently deliver high-quality parts on time and at competitive prices. Reliable component sourcing is crucial for maintaining the quality of the final product and meeting customer expectations.
Assembly sequence: Develop a clear and efficient assembly sequence that minimizes handling, reduces waste, and optimizes the use of resources. This may involve creating a detailed assembly plan and using tools like value stream mapping to identify and eliminate bottlenecks. An efficient sequence is essential for producing a quality product efficiently.
Workforce training: Invest in comprehensive training programs for your assembly line workers to ensure they have the necessary skills and knowledge to perform their tasks effectively. This can help reduce errors, improve productivity, and enhance product quality. Well-trained employees are vital for maintaining high standards in the manufacturing process.
Continuous improvement: Implement a culture of continuous improvement in your assembly processes. Encourage team members to suggest idea for streamlining operations and regularly review and update your processes to incorporate best practices for manufacturing and new technologies. Continuous improvement helps in adapting to industry changes and meeting evolving customer expectations.
Considering these factors ensures that the final product meets quality standards, is produced efficiently, and aligns with customer expectations, thereby supporting the growth and success of the business.
The Steps Involved in the Final Assembly Process of Product
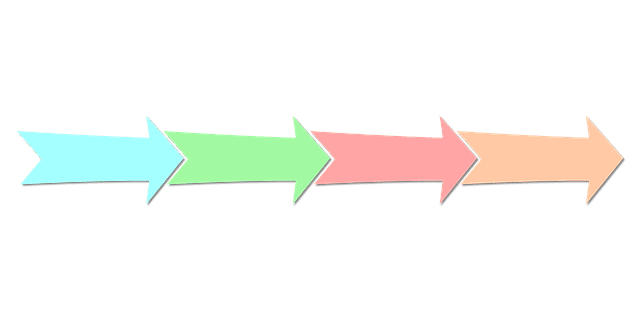
The final products assembly process typically involves the following steps:
Component preparation:
Ensure that all necessary components are available, inspected for quality, and properly organized for the process.
Sub-assembly:
If required, pre-assemble parts certain components into sub-assemblies to simplify the final assembly process. These assemblies may be comprised of mechanical, electrical, or software components.
Assembly lines setup:
Configure the assembly lines according to the predetermined sequence, ensuring that all necessary equipment, tools, and materials are in place.
Assembly process:
Begin the assemble process, following the established sequence and quality check procedures. This may involve the use of automated machinery, robots, or manual labor, depending on the assembly methods or manufacturing processes chosen.
Quality inspection:
Conduct regular quality inspections throughout the process to identify and correct any defects or inconsistencies. This may include visual inspections, functional testing, or other quality check measures.
Packaging and labeling:
Once the product is fully produce and has passed all quality inspections, package it according to customer specifications and apply any necessary labels or branding.
Final testing:
Perform a final round of testing on a sample of finished product to ensure they meet all required performance and quality standards.
Shipping and delivery:
Prepare the finished product for shipping and coordinate with logistics providers to ensure timely and efficient delivery to customers.
Tips for a Smooth and Successful Right Arrow Final Product Assembly Manufacturing Processes
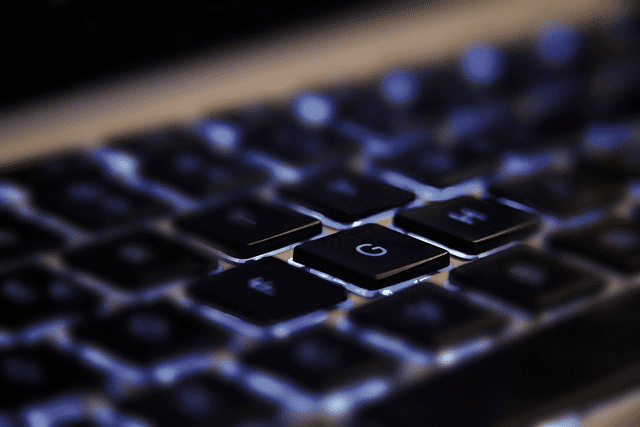
To ensure a smooth and successful final products assembly process, consider the following tips:
Plan ahead:
Develop a comprehensive assembly plan that outlines all necessary steps, resources, and timelines. This can help ensure that everyone involved in the process is on the same page and working towards a common goal.
Communicate effectively:
Foster open and clear communication among all team members involved in the assembly process. This can help identify and resolve issues quickly, as well as promote collaboration and innovation.
Leverage technology:
Utilize the latest technology and automation tools to streamline your assembly processes and improve efficiency. This may include the use of robotics, machines vision systems, or other advanced manufacturing technologies.
Monitor and measure:
Establish key performance indicators (KPIs) to monitor and measure the effectiveness of your assembly processes. This can help identify areas for improvement and track progress over time.
Foster a quality culture:
Promote a culture of quality throughout your organization, from the assembly line to upper management. Encourage everyone to take ownership of product quality and continuously look for ways to improve.
Manage inventory effectively:
Implement an effective inventory management system to ensure that you have the right components and materials available when needed, without overstocking or running out.
Train and empower employees:
Produce comprehensive training and development opportunities for your assembly line workers and empower them to produce decisions and take ownership of their work. This can help boost morale, reduce turnover, and improve overall performance.
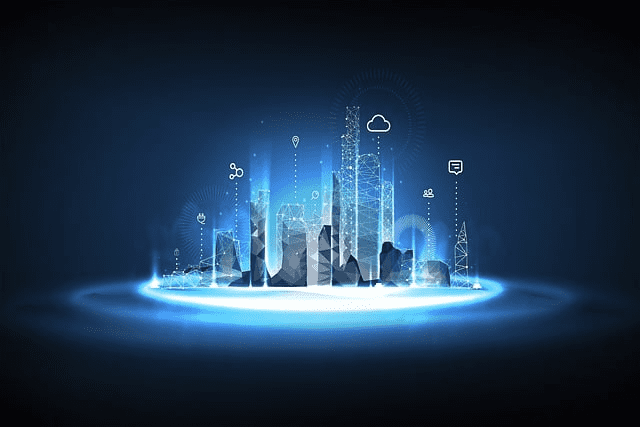
By following these tips and implementing best practices for manufacturing throughout your finished product assembly process, you can streamline operations, improve quality, and ultimately bring products to market faster and more efficiently. To learn how to streamline manufacturing process and supply chain management to bring products to market faster by increasing efficiency, reading our best practices for manufacturing is a great place to start.
Examples of an an assembly process may involve combining individual components, such as mechanical, electrical, or software parts, into a completed product. By understanding the different types of assembly methods and implementing effective practices for manufacturing supply and quality check measures, manufacturers can manufacture and optimize their assembly processes. They can be produced high-quality finished products more efficiently, saving time and money in the long run.
Final Product Assembly FAQ
1. What is Final Product Assembly?
Final product assembly is the process of combining individual components and materials into a finished product during manufacturing. This crucial step involves various assembly methods, such as automated machinery, robotic assembly, and manual assembly, to increase efficiency and quality control. The goal is to produce a quality product that meets customer expectations.
2. What is a Bill of Material (BOM) in Final Product Assembly?
A Bill of Material (BOM) is a detailed list of all components required to assemble the final product. This document ensures that all necessary parts are available for the process, facilitating the smooth processing and production of the end product. The BOM is a key component of the manufacturing system.
3. What Types of Assembly Lines Are Used in Final Product Assembly?
Assembly lines for producing the final product can include machines, robots, and human workers, each performing specific tasks. These lines are designed to move components efficiently through various stages of production, optimizing the process and ensuring the finished product meets quality standards.
4. Why is Supply Chain Management Important in Final Product Assembly?
Effective supply chain management ensures the timely procurement and delivery of materials and components. It helps reduce costs, minimize waste, and improve overall efficiency. This management is crucial for producing a quality product that meets customer expectations and industry standards.
5. How is Quality Control Implemented in Final Product Assembly?
Quality control involves regular testing and inspection of components and the finished product to ensure they meet required standards. By catching defects early, manufacturers can avoid costly rework or product recalls, saving time and money while delivering a quality product that meets customer expectations.