Thinking about the manufacturing test strategy early in the design process is key to creating an effective and efficient test. It can be a balancing act to have adequate test coverage while also controlling the manufacturing costs associated with operating the test procedures.
The circuit designer should plan for how the product is tested and how much self-test, diagnostic capability, component isolation, boundary scan, and node access will be designed in. As the design proceeds to layout, items such as tooling holes, probe access, probe density, component accessibility, and clearances should be considered.
At some point, a decision must be made concerning the manufacturing test strategy and platform. There are three popular test options: In-Circuit Test (ICT), Flying Probe, and Functional. Making this decision early in the design can avoid costly design rework or acceptance of reduced test coverage later.
In-Circuit Test (ICT)
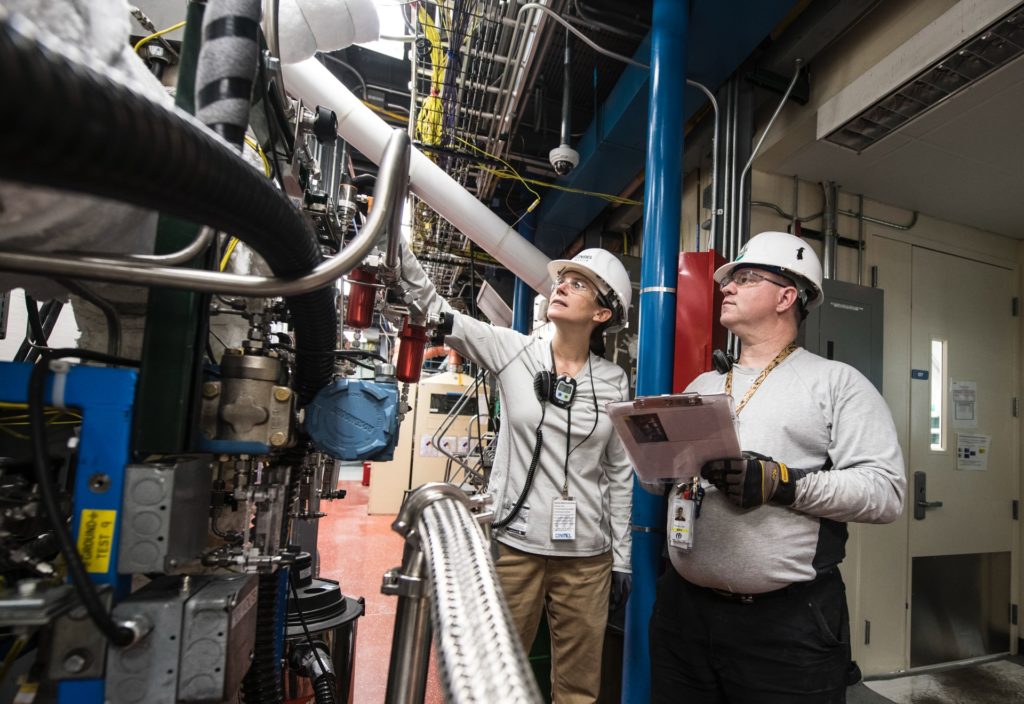
ICT is often a general-purpose test platform like HP3070 series or Genrad/Teradyne with a bed of nails fixture. The advantages of ICT include low per-piece cost, exceptional coverage (if designed for test), power-up test for both analog and digital functions, integrated boundary scan, and device programming. The downside is the initial cost of test development and dedicated fixtures. ICT can be very cost-effective overall for high-volume long-life products compared to the development costs of a dedicated functional test and the higher per-piece test costs of other options.
Flying Probe
The flying probe provides an option for low volume short life products. Programming is often derived from CAD data and there are no fixture costs. Thus, the development cost is low, but the per-piece cost is often much higher than ICT due to higher test times. The flying probe is very effective at the identification of missing, wrong, reversed, and defective for two and three pole components. The approach is most effective for manually loaded through-hole assemblies. Some Flying Probe testers also provide for JTAG device programming and boundary-scan for IC validation. The flying probe is frequently used to accelerate prototype validation – when turning on a new design it is helpful to have high confidence the assembly was correct and Flying Probe is a low-cost means to that end.
Functional Test
Functional Test can cover a very broad range of options from a simple power-on self-test to the installation of the assembly into a product and execution of product level tests. This approach often provides the very best coverage and validation but at a high price. Unless the dedicated equipment is automated, the per-piece time tends to be high and the test development time can be significantly higher than ICT or flying probe.
In some cases, like high energy power supplies or products with safety issues, a mixed approach may be in order. For example, you may wish to validate components on Flying Probe before you power-up an assembly in a product based functional tester to prevent potential damage to equipment or expose personnel to an unsafe condition.
It is important to make a test strategy decision early in the design process and Vergent products can help with cost/benefit analysis of the various options while also providing design for test and test development services.